Benefits of additive manufacturing and 3D printing in customised medical devices
- Increased design freedom – customised geometry
- Economic low volume production
- Patient-specific devices that can be modified as the user grows or requirements change
- Manufacture at the point of need and accelerated product development
- Integration of additional function
- Weight reduction and increased patient comfort
Prosthetics and soft robotics
Our cross-disciplinary team is developing new designs and methods of manufacture of upper and lower limb prostheses to support independent living.
Combining the expertise from biomechanics, additive manufacturing, robotics and human factors, we are working to improve the functionality and patient comfort and reduce the cost of these devices. (Experts: Ruth Goodridge, Ian Ashcroft, Donal McNally, David Branson) Our projects include:
- Exoskeletons for lower limbs, with sophisticated sensing, actuation and control for enabling effective and comfortable rehabilitation, functional restoration and long-term assisted living. They will be targeted at stroke patients, leading to more independence, with less risk of falling.
- The use of state-of-the-art multi-material additive manufacturing and design optimisation techniques for the production of high functioning upper limb prosthetics
Implants
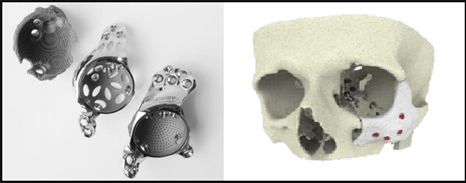
We are developing a range of implants to support different parts of the body, taking into account biocompatiblity, interfaces, metrology, and behaviour.
Projects include:
- Working with Nottingham University Hospitals NHS Trust (City Hospital) we are developing annuloplasty wings to help keep the heart operational. (Ruth Goodridge, Donal McNally)
- Maxillofacial implants to support facial reconstructon (Joel Segal)
- Surface functionalisation of biomedical Implants using self-assembled Monolayers (Ruth Goodridge, Richard Hague)
- Metrology for biomedical implants (Donal McNally, Richard Leach)
- Due to the potential for low cost bespoke implants, we are now exploring the workflow for the manufacture of these implants in lower income countries
Tissue scaffolds
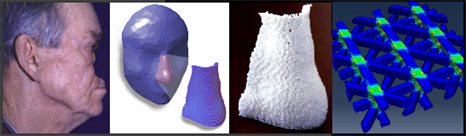
We are developing new techniques and applications for bioprinting of tissue engineering scaffolds, from biological characterisation to engineering design.
- Bio-printing personalised scaffolds for nasal reconstruction (Joel Segal, Kevin Shakesheff)
- 3D-Printing of Gelatine based structures for biomimetic
applications (Felicity Rose, Ricky Wildman)
- 3D ink-jetting of hydrogels, cells, proteins and other biocompatible materials (David Grant, Colin Scotchford, Donal McNally)
Personalised drugs
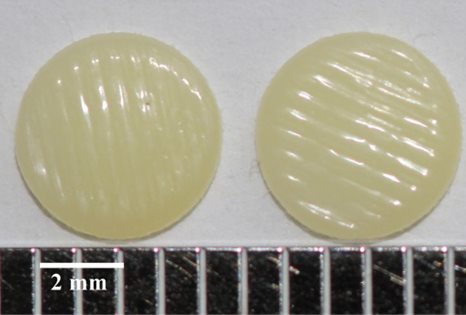
Working with Astra Zeneca and GlaxoSmithKline, we are developing capabilities to print bespoke drugs. The injet technology will allow the dose and the matrix to release the drug when and where it is needed, from fast disintegrating tablets, fast melting tablets, to polypills.
(Ricky Wildman, Clive Roberts, Morgan Alexander, Chris Tuck, Richard Hague)
http://eprints.nottingham.ac.uk/44295/1/1-s2.0-S0168365917306892-main-PW.pdf
Sensors and conductive parts
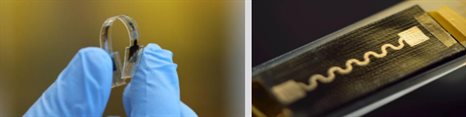
Using ink jet printing, we can create multi-functional parts by inkjet printing functional materials for electrical, mechanical, pharmaceutical and biological applications. These include:
- Electrical and electronic device applications
- 3D multi-functional parts with embedded electronics eg conductors, semiconductors and dielectrics)